Using more recycled materials to build our cities
University of Melbourne experts have been working with industry to find new uses for large volumes of recycled waste plastics.
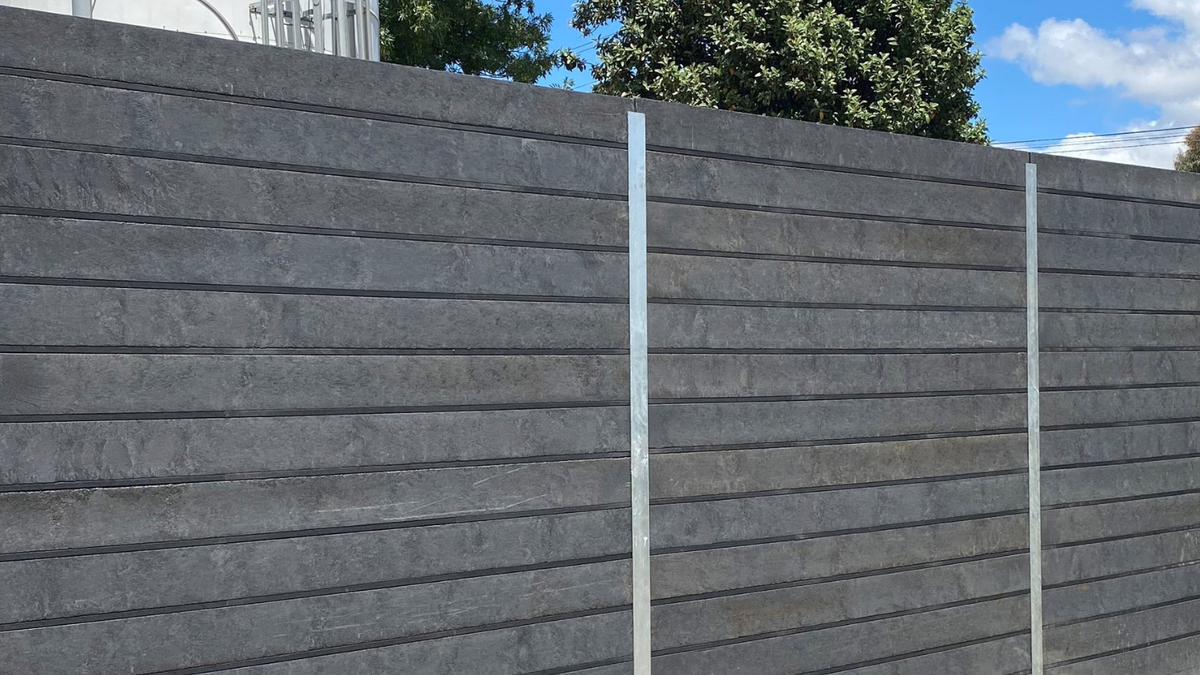
First published by the University of Melbourne
When it comes to finding new ways to use old plastics, bigger really is better. After all, the more plastic waste used in a material, the less ends up in landfill. A promising emerging technology from Mildura-based Integrated Recycling, tested by University of Melbourne experts, could be used to build very large structures like noise barriers, helping to keep hundreds of tonnes of plastics out of the ground.
Their patented material, Polytensilate, contains around 85 per cent waste plastics – most of which comes from agricultural uses like protective films, pipes and polystyrene packaging for fruits and vegetables.
“Agriculture in Australia uses about 110,000 tonnes of plastics a year,” says Integrated Recycling’s General Manager, Stephen Webster.
“There is growing awareness and increasing government support to recover and repurpose plastics, including agricultural plastics.”
Transforming waste plastics into products
Integrated Recycling developed Polytensilate more than 15 years ago to transform waste plastics into a range of landscaping, industrial and infrastructure products, such as Duratrack recycled plastic railway sleepers. The Victorian Government’s Recycle First policy is driving greater use of recycled materials in the state’s infrastructure projects and creating new opportunities to find new uses for recycled materials.
Working with University of Melbourne geotechnical engineering experts Associate Professor Mahdi Disfani and Dr Amirhassan Mehdizadeh, Integrated Recycling has been testing the material’s use in noise barriers and retaining walls.
By tweaking the Duratrack formulation, they have manufactured lightweight Polytensilate panels that show promising results for both new applications.
“It has been great to have the opportunity to do some applied research to see how our material performs under new applications,” says Mr Webster.
Associate Professor Disfani and Dr Mehdizadeh put the panels through their paces in their infrastructure engineering lab at the University.
“We assessed the panels as noise barriers and retaining walls, testing characteristics like noise absorption, fire resistance, UV resistance and ability to sustain mechanical loads,” says Associate Professor Disfani.
"The panels went through a series of robust and extensive tests and we were very comfortable with their performance."
From plastic to noise barrier
The ‘real-world’ performance of the panels as noise barriers is now being trialled at Integrated Recycling’s Reservoir factory, to reduce the facility’s noise impact on residential neighbours.
The University of Melbourne team will measure the product’s performance over coming months. In a market saturated with timber and concrete solutions, the team is optimistic that the Polytensilate panels will prove an effective and environmentally-friendly alternative.
“Recycled plastic has a few notable advantages over timber or concrete, beyond just its environment credentials,” says Associate Professor Disfani.
“It is light, but still performs very well in terms of noise reduction. It also has a long life out in the elements. And this product is fully recyclable at the end of its life, so it’s a truly circular product.”
Consuming waste plastics
Another big benefit is the potential for Polytensilate products to consume very large volumes of recycled waste plastics. For example, if an infrastructure project requires 500 metres of noise barrier, it would equate to 3000 square metres of panels.
“That would require tens of tonnes of waste plastics, which translates to millions of plastic bags, for example,” says Associate Professor Disfani.
“The promise of this product is significant.”
Mr Webster is hoping the trials will contribute to a wider change in behaviour, as recycled materials become more accepted in the building industry.
“We’d like to help users understand that these non-traditional materials can be used in traditional ways,” he says.
“Valid science and performance data is the best way to overcome inertia to change. Ultimately, we want to change patterns of behaviour so that the environmental impact of a product and its whole-of-life performance is taken into consideration.”
This project is supported through a Sustainability Victoria grant from the Victorian Government’s Recycling Industry Strategic Plan Fund. Sustainability Victoria is a government authority that facilitates and promotes sustainability in the use of resources.